BioGuard pioneered the idea of computerized pool water analysis and we have continued to research and refine the process. Today, ALEX, our computerized water analysis system, provides accurate results in an instant. All you have to do is bring in a water sample from your pool or spa to your local BioGuard Dealer and you’ll receive personalized step-by-step instructions for start-up, closing and maintenance. It’s that easy!
- Current driver software: OPTIMA and IDEA. Nano, EXPERT, PICO, ALEX IDEA configuration software.
- Epson Remote Printer Driver. This driver allows you to print to an Epson email-enabled printer anywhere in the world right from your computer. Important: In addition to the Epson Connect Printer Setup Utility above, this driver is required for remote printing. Not sure if have a 32-bit or 64-bit edition of Windows?
- Operating system: Windows ME, Windows 2000, Windows XP, or Windows 7 or higher (32-bit or 64-bit). Windows 95 and Windows 98 are not supported. CPU: Pentium-4 2.5 GHz with a wideband radio, or 1 GHz with a 3-kHz radio.
How is BioGuard’s ALEX water testing different?
Here accuracy counts and we have it! Our test is fast and much more accurate than a simple dip of a test strip at poolside or a self-driven analysis using a computer or mobile application. That’s because we test for several parameters beyond the basics to understand how they may be influencing each other in order to avoid trial and error. Being right the first time saves you time and money.
On top of that, our local water care experts have been trained and certified. They will walk you through the results and are happy to explain anything you might have questions about. Our ALEX recommendations will be sound based upon the way you care for your pool and the accumulated knowledge of all your previous water tests.
Our goal is that you will not only be satisfied with the performance results, but that you gain confidence in the products and advice you receive.
Why should I test my water?
Water testing is important to achieve and maintain a safer swimmer environment. Water chemistry can be quite complex with all the different factors.
Download the latest XP-Pen drivers, User Manual, and software for Linux/ubuntu, Windows 7 /8 /10 and Mac operating system. This is XP-Pen's official website. A hardware driver is a small computer program that allows your computer to interact with XP. Our newest GeForce Game Ready driver brings you day-one support for Half-Life: Alyx, Resident Evil 3, Ghost Recon Breakpoint’s Ghost Experience update, and the addition of NVIDIA DLSS 2.0 to Control and MechWarrior 5: Mercenaries. To download and install, simply fire up GeForce Experience and click the 'Drivers' tab.
For example, if your water is out of balance or your pH isn’t in the right range it can cause problems, such as equipment damage and swimmer discomfort. Balanced water also contributes to the effectiveness of other products so it is an important start to your water care regimen.
How often should I get my water tested?
We recommend you get your water tested when you open and close your pool. In season it is recommended to test every two weeks or minimum at least once a month. The amount of use and environmental factors can easily change water conditions and staying on things will prevent issues that may prove troublesome to correct if neglected.
Why did we name our water testing software ALEX?
ALEX stands for analysis expert, which is who we are.
Firmware upgrade
You can check new versions and upgrade firmware from the SimpleBGC GUI application. Download latest GUI, connect board and upgrade firmware at the Upgrade tab. See user manual for more info.
/!macOS users: if you experience problems connecting to the board, see description below
Detailed changelog file(35Kb1.09.2020)To test the latest beta-version of firmware, download the GUI 2.70 b1 and upgrade firmware enabling the 'Check for beta versions' flag.
2.70b0 — latest stable version
- GUIWindows, macOS, Linux
- SimpleBGC_GUI_2_70b0.zip(19Mb1.09.2020)
- User ManualEnglish
- SimpleBGC_32bit_manual_eng.pdf(2Mb8.09.2020)
- User ManualRussian
- SimpleBGC_32bit_manual_rus.pdf(2Mb18.08.2020)
- User ManualFrench by marcg (for previous version)
- SimpleBGC_32bit_manuel_2_6x_FR.pdf(2Mb14.02.2017)
- User ManualChinese by Zhang Yi (for previous version)
- SimpleBGC_32bit_manual_2_6x_chn.pdf(2Mb20.03.2017)
Release notes
System performance
- Many bugfixes in firmware and GUI.
- New «jerks limiter» parameter, which limits the rate of change of acceleration to get smooth
S-curve in a speed profile - IMU AHRS calculations are improved; added various options to apply correction from the external,
high-grade GPS-aided AHRS/IMU («External IMU» tab) - Encoder firmware: option to change the width of the software limiter
break-down area for each motor - Solved a problem with the forbidden Euler angles near gimbal lock (ROLL=90° for PITCH-ROLL-YAW, PITCH=90° for ROLL-PITCH-YAW). Now all axes support fluent 360° rotation («RC» — «Gimbal lock smooth transition»)
- «Extended» family: improved work near gimbal lock condition by smart correction of the middle motor position, controlled by the new parameter GLOCK_MID_MOT_POS_CORR_RATE
- Encoder firmware: max. available motor torque is increased by 15% due to the improved FOC algorithm.
Service functions
- New option «Service» — «Execute action at system start» to activate any function by special combinations of RC/joystick sticks when turning system ON.
- New option «Service» — «Profile sets» allows creating sets of profiles and switching between them; additional «BACKUP» slot allows automatically to restore the most critical settings if the configuration in EEPROM becomes corrupted for some reason.
- «Force to a new position by hands» supports snapping to fixed angles of 45° step.
- Option to connect an external LED and duplicate the main LED functionality («Service» — «Buzzer and LED»)
- Option to configure a «parking position» — when the selected motor goes outside the
user-defined working range, motors are turned OFF automatically, and turned ON again after returning back to the working range («Encoders» — «Do parking outside limits»). User-defined melodies («Service» — «Custom melodies»)- On a profile switch, the profile number is signaled by the number of beeps of the buzzer. The LED blink pattern can be configured to show the current profile.
- New options linked to the mode button's «press» action: «Temporarily force follow» for a fast camera re-position, and «Temporarily disable follow mode» for a quick handle reposition.
- New option «Service» — «Camera
upside-down as working position»: when the gimbal is started with the camera, or frame, or both positioned upside-down, don't try to move to a normal position but keep working with the 180° offset. - New option «Tripod mode» for gyro drift compensation when gimbal's frame is steady
- New parameter «Hardware» — «Misc. hw settings» — «Motor startup delay, ms», to energize motors on system initialization with delay
«Extended» family only:
- Option to collect basic system statistics and store to EEPROM for further analysis.
- Option to connect the 4th mechanical axis to optimize frame position (servo motor with the PWM input, or CAN_drv + BLDC motor + encoder)
- Scripts: add support of temporary variables and basic math operations for using in other commands and for data logging in GPS_IMU; added IF.. GOTO command for program flow control and cycles;
Remote control and new input options
- New signal source «Step signal source»: its value is incremented by the fixed steps, triggered by the «high» or «low» levels of any assigned RC signal source, allowing to control many system parameters (by linking this signal source to adjustable variable) remotely, and store the set value permanently in EEPROM.
- Extended calibration of 5 arbitrary RC inputs against «min», «max» and «neutral» points.
- Option to automatically replace the ADC 1..3 signal source to another RC source, if a device on the ADC input is not connected (auto-detection of the floating pin state)
- Up to 5 extra push buttons are supported (momentary or latching), allowing a flexible configuration of their actions («Service» — «Extra buttons»)
Safety functions
- Option to turn OFF motors when they are fully loaded for a long time, to prevent damage when working gimbal is put in the bag, for example («Service» — «Max. time to work under full load»).
- Menu command «Motors OFF safely» prevents the camera from falling if it's not well-balanced: camera slowly goes to the steady position where motors are turned OFF.
- «Overall current limit» — if this value is set to non-zero, the controller tries to estimate an overall current consumed by motors and limits if exceeded, preventing battery overload and limiting the controller's overheat.
Advanced calibrations («Extended» family)
- Fully automatic multipoint calibration of the accelerometer.
- Current sensor can be
re-calibrated - Gyroscope biases online calibration using the external IMU as a reference
- Advanced calibration of 12 parameters of gyroscope using the external IMU as a reference
- Advanced
multi-point calibration of 21 parameters of the main IMU sensor (accelerometer and gyroscope) w/out special equipment - New tool for the automatic encoder
non-linearity calibrationin-place using IMU sensor - Motor cogging correction: GUI displays calibration process and resulting LUT
GUI improvements
- «Analyze» tool can provide more information about system performance (new «Sensitivity» curve).
- New powerful tool «Optimize» (in «Analyze» tab) allows automatically find the best set of PID parameters suitable for multiple gimbal positions or payloads, satisfying the given requirements for performance vs. stability and the given stability margins in frequency domain. It's an improved replacement for the old automatic PID tuning algorithm.
- New function «Copy parameters between profiles».
- Add a group of buttons to indicate the currently active profile and to switch between profiles faster.
- Better compatibility with the latest Java 8, 9 and latest OS versions.
- Fixed appearance on
high-DPI displays. - Firmware upgrade over TCP/IP and UDP is supported.
New periphery and hardware support
- Support of the new IMU sensor ICM20602 and magnetometer HMC5983, QMC5883L (wrongly labeled «HMC5883L» on some breakout boards).
- A variety of new encoders. The full,
up-to-date chart of all supported models is available in the Encoders Manual. - Tilted middle motor allowed in the mechanical configuration.
«Extended» family:
- New CAN_Drv motor driver with high currents capabilities, running
fully-featured FOC algorithms and allowing to move motor driver closer to a motor in a modular system based on a common CAN bus. - Add support of external IMU sensors: Vectornav VN100, VN200, Inertialsense uAHRS, Basecam Electronics GPS_IMU v.1.2.
- Add support of KVH FOG gyroscopes.
- Add an option to connect a magnetometer sensor directly to I2C port of the CAN_IMU sensor (requires the latest firmware).
- New order of hardware axes «CAM-ROLL-YAW-PITCH».
Serial API
- The event subscription model in the CMD_DATA_STREAM_INTERVAL allows the external device to track various gimbal events.
- Option to forward all serial API commands from all ports to the currently connected port for a debugging.
- Version 2 with better error protection (CRC16 instead of 8-bit checksum).
- Documentation is improved; Many commands got extended modes.
UAV connection via MavLink protocol
- Allow specifying new mounting positions for a flight controller: «Below the middle motor» and «On the camera platform.».
- «MavLink control mode» — use it to disable the MavLink control and switch to regular RC/Follow control mode. Also, modes can be switched by the corresponding adjustable variable.

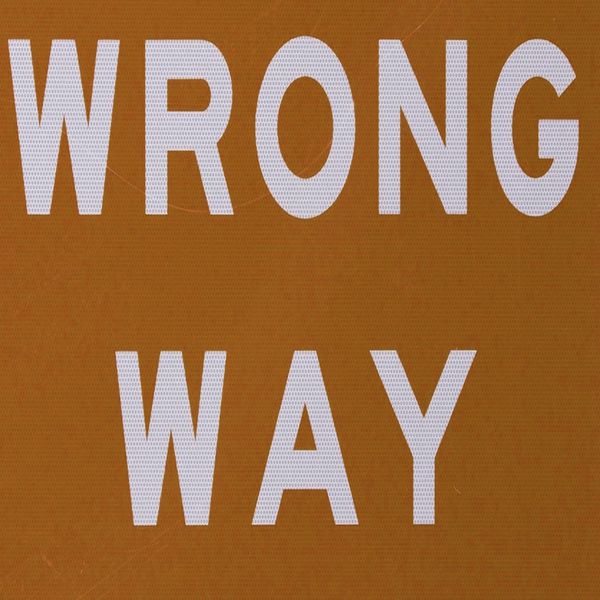
2.63b0
- GUIWindows, macOS, Linux
- SimpleBGC_GUI_2_63b0.zip(8Mb1.06.2017)
- User ManualEnglish
- SimpleBGC_32bit_manual_2_6x_eng.pdf(2Mb8.09.2020)
- User ManualFrench by marcg (for previous version)
- SimpleBGC_32bit_manuel_2_6x_FR.pdf(2Mb14.02.2017)
- User ManualChinese by Zhang Yi (for previous version)
- SimpleBGC_32bit_manual_2_6x_chn.pdf(2Mb20.03.2017)
Release notes
Hardware support
- Motors with encoders having a freedom of rotation more than 360º are supported: system will automatically search the nearest limit and return to home position.
- New option «Hardware» — «IMU Sensor» — «Misalignment correction»: allows correcting misalignment of the IMU sensor's internal axes relative to the camera's optical axis and motor's axes. Calibration is supported.
- New CAN_IMU sensor is supported via CAN or I2C interfaces.
- New encoder type is supported: RLS «Orbis» with the PWM 459Hz and SPI interfaces.
- Different type of encoders can be mixed in one system: PWM and SPI, PWM with different frequencies, SPI of a different type, etc.
- New parameter «Hardware» — «Outer motor tilt angle» that provides a support of
non-orthogonal motor configurations. - Encoder calibration is improved: allows to set the range of rotational angle and can be done in abnormal positions.
- New option to move all motors to a home position at startup (encoder firmware only).
- New menu command to switch into portrait mode (ROLL=90) and back. System keeps this mode on profile switching.
- 1-, 2-axis system: option to switch to different stabilization axes automatically at startup or by changing profiles.
- New flag «Hardware» — «Don't power ON motor at system start».
New parameters and functions
- New group of parameters «Advanced» — «Automated motion tasks» to set the speed and acceleration for automatically executed movements like «Look down», «Home position», etc.
- Implemented a calibration of motor
non-linearities to improve stabilization quality by compensating the cogging effect (supported by the «Extended» and «Pro» boards only) - New type of Adjustable Variables: 'relative'. It acts as a multiplier for applying to a
user-editable parameter. - New type of Adjustable Variables:
look-up table. Allows a better control when setting dependency between signal and variable. - New parameter «Follow mode» — «Follow range» allows setting the angle that defines the active range from zero to full speed in the follow mode.
- New option «Follow» — «Disable follow mode by holding menu button»: use it to disable follow mode temporarily by pressing and holding menu button without the need of switching profiles.
- New menu commands «Setup and start
time-lapse motion», «Repeat time-lapse». Use it to programtime-lapse motion sequence in few seconds without the need of GUI connection. Excellent tutorial fromTomasz Walczak. - Scripting language: new command «SET_ADJ_VAR» with example of using it for
drift-free time-lapse shooting
GUI improvements
- Parameters was
re-arranged and better grouped by their meaning - New menu «View» — «View level» to choose the level of complexity from «Basic» to «Developer». Developers can further adjust it in the configuration file «conf/view_level.properties».
- New backup manager that allows to save a snapshot containing all settings and calibrations to the cloud; One password-protected 'factory' and up to 3 'user' backups are supported.
- New option to save settings into .profile files based on templates. Can be used to selectively update parameters when copying the configuration from one system to others.
Bugfixes
- Serial port communication might impact stabilization in case of poor wireless connection.
- MavLink gimbal control was reversed for the YAW axis
- «Tiny rev.A» can not connect to the GUI via USB port
- GUI does not work after upgrading CP210x drivers to version 6.7.4 (done automatically by Windows 10)
2.60b4
- GUIWindows, macOS, Linux
- SimpleBGC_GUI_2_60b4.zip(8Mb7.09.2016)
- User ManualEnglish
- SimpleBGC_32bit_manual_2_6x_eng.pdf(2Mb8.09.2020)
- User ManualFrench by marcg
- SimpleBGC_32bit_manuel_2_6x_FR.pdf(2Mb14.02.2017)
- User ManualChinese by Zhang Yi
- SimpleBGC_32bit_manual_2_6x_chn.pdf(2Mb20.03.2017)
Release notes
New features
- New enhanced PID auto-tuning algorithm:
- Fast and reliable;
- Finds most optimal PID gains to minimize error of stabilization and prevent self-excitation;
- Flexible: can tune PID from zero or slightly adjust gains starting from the current values;
- Able to tune other parameters, like low-pass filters;
- Has safety interrupts to prevent damage in case of wrong system operation;
- No GUI connection is required - can be run by the menu button command;
- Allows to update PID settings in all profiles;
- New settings 'Filters' - 'D-term LPF filters' that can help to remove high-frequency oscillations in some setups and allows to set greater PID gains
- Notch filters are extended: can be used as peak filter; gain is set in dB instead of %
- Acceleration limiter setting is split per-axis
- New types of encoders are supported for YAW axis in the regular firmware: PWM and I2C.
- New option 'PID Gain multiplier' to extend the range of PID settings or link PID gain to adjustable variables, to tune it on-line by the analog potentiometer or RC.
- Serial API was extended by many new commands
- Option to disable of using gyro signal from the frame IMU for stabilization, but keep it for a frame angle detection; option to pass it through low-pass filter with adjustable cut-off frequency. Both options are useful in the case of high level of vibrations on the frame.
- Add a support of MavLink protocol for Ardupilot FC connection (beta state), that allows to increase a precision of stabilization and control over gimbal in automated missions.
- Option to backup/restore IMU calibrations to a file
- (Encoder version) Motor over-heating protection is improved: more precise model, virtual temperature is shown in the GUI to simplify tuning process; new safety action: alarm and cut-off motors
- (Encoder version) 'Encoder field offset' parameter is calibrated automatically, no frame movement is required.
- Parameter 'Magnetic linkage of a motor' will improve precision of stabilization; new auto-calibration function for this parameter
- Angle of motors can be used as a source in the 'Adjustable Variables' to set a dependency of the system parameters on the camera-to-frame relative position, set by the inner (counting from the camera) and the middle motor's angles
- Option to enable 3rd serial port: UART2 (Rx: AUX3, Tx: n/c); option to swap pins with the RC_SERIAL port (Rx: RC_ROLL, Tx: RC_YAW). In the encoder-enabled version, ports are swapped by default.
- New menu commands to switch to selfie mode by rotating camera 180 degrees from current position or 0/180 relative to home position, by the YAW axis.
- Several new commands in scripting language; option to use dynamic variables linked to the RC signal sources
- Option to automatically switch to upside-down mode (both frame and camera) and auto-rotate camera when frame is rotated +-180 degrees over PITCH axis.
Bugfixes
- Fixed problems with USB connection in 'Tiny' boards
- RC control is slightly improved: smoother 'Angle' mode, no overshoot after fast breaks
- Script parser: properly handles speed below 0.07 degree/sec for very slow time-lapses
- Fixed problems with the firmware upgrade under modern macOS versions
- Many minor improvements of the system performance in various conditions
2.50b3
- GUIWindows, macOS, Linux
- SimpleBGC_GUI_2_50b3.zip(8Mb14.04.2015)
- User ManualEnglish
- SimpleBGC_32bit_manual_2_50_eng.pdf(1Mb6.05.2015)
Release notes
- User-written scripts (see Language Reference and user manual)
- IMU temperature calibration and compensation.
- New tool 'Analyze' to make an analysis of system response.
- Notch filters have adjustable gain (0…100%)
- 'Motor outputs' settings group is changed to per-profile basis
- GUI and firmware support Bluetooth Low-Energy (BLE) module communication (experimental)
- New setting group 'Outer PI controller' to adjust values for outer (cascade) PI controller (default value is 100 suit most setups)
- New option 'Swap frame and main sensors' to use frame IMU as main IMU and vice versa
- New option 'Gyro dead band' to cut off gyro noise around zero (that may be audible as 'white noise' in heavy setups)
- New option 'I2C high-speed'. Use it carefully: high-speed mode may cause I2C errors.
Bugfixes:
- Problem with SSL connection during firmware upgrade is solved
- Frame upside-down command loads default profile after reset
- Frame upside-down detection doesn't work if 'skip gyro calibration' is disabled.
- Acceleration limiter does not work properly with the big speed setting in the 'Follow' mode: camera overshoots target position
ENCODER version:
- New encoder type 'Analog'. See updated manual //www.basecamelectronics.com/files/SimpleBGC_32bit_Encoders.pdf
- Different encoder types may be assigned to different axis
- Option to adjust sound volume in the 'beep by motors' mode in the 'Service' tab
- Bug fixed: upside-down frame switching is not correct
- Several bugs fixed related to encoder calibration
ALEX Driver Download
2.56b7
- GUIWindows, macOS, Linux
- SimpleBGC_GUI_2_56b7.zip(8Mb20.01.2016)
- User ManualEnglish
- SimpleBGC_32bit_manual_2_5x_eng.pdf(1Mb29.06.2016)
Release notes
New hardware:
- Support of ICM20608 gyroscope+accelerometer sensor.
- New option 'I2C high-speed'. Use it carefully: high-speed mode may cause I2C errors.
- Support for saving and restoring of calibration data to the IMU's EEPROM (if present).
- Support of analog encoder (rotary position sensor) on YAW axis in the regular firmware.
- New option 'Advanced' 'Order of hardware axes' that supports several configurations besides the standard 'Camera PITCH - ROLL - YAW' configuration.
- Support of magnetometer sensor (compass) to prevent drift of gyroscope. Can be combined with the frame IMU or the main IMU.
Control algorithms:
- New setting: 'RC' 'Order of Euler angles' that allows extending the possible trajectories of a camera and the range of working angles.
- Improved the precision of RC control in the 'Follow' mode
- New option 'Follow' 'Apply an offset correction when an axis is not following.'
- New option 'Follow' 'Follow rate inside dead-band' to apply very soft control to keep camera always in the center of the dead-band.
Sensors calibration:
- Regular calibration of Accelerometer and gyroscope does not discard the results of temperature calibration but improves it.
- ACC calibration at 'normal' Z-top position does not discard the results of 6-point calibration.
- Magnetometer (compass) calibration was significantly improved:
- you do not need a GUI connection (allows to calibrate in the field by menu button);
- an ellipsoid approximation is used;
- New option to skip gyro calibration if gimbal is not fixed well during startup: it allows to start with fresh calibration for best quality, or to start immediately with the previous calibration.
IMU improvements:
- Advanced algorithms for correction of mutual drift in both IMUs.
- '2nd IMU above YAW' position is more reliable now.
- New option 'ACC low-pass filter' that helps to improve the stability of the IMU angles. Under dynamic conditions like motion with short lateral accelerations.
Other functionality:
- New adjustable variables GYRO_HEADING_CORRECTION and FRAME_HEADING_ANGLE that helps to manually correct YAW axis drift.
- New option 'Advanced' 'Set to the normal position on profile switch'.
- Better handling of high-speed control from scripts.
- Improved the range of working angles in 1- and 2-axes systems, making use of 2nd IMU or encoders; all possible 2-axes configurations are supported now.
- New menu command: 'Untwist cables'.
- New checkbox 'Advanced' 'Upside-down PITCH auto-rotation' to turn camera when turning frame upside-down.
- New option 'Follow' 'Use frame IMU, if possible' to use 2nd IMU for the 'Follow Mode' control, to make it more reliable.
- New menu command: 'Center YAW axis' to move a camera to the neutral position by YAW.
- New menu command: 'Level Roll, Pitch to the horizon'.
- New option 'Service' 'Blink profile number' - onboard LED will show currently selected profile.
- Proper handling of 'gimbal lock' condition - when YAW and PITCH motor axes are parallel.
- (GUI) New 'Emergency stop' option (stop motors in case of the big rate of I2C errors).
- (GUI) Serial-over-UDP connection is supported to configure remote devices via a network (WiFi, Ethernet, Internet).
- Menu button pressed 12 times in series will reset 'Serial speed' setting to default value 115200.
- OuterP, OuterI gain increased 5x times.
Encoder-enabled firmware:
- Option to emergency stop if the motor angles reported by the encoder differs a lot from the angle reported by the 2nd IMU.
- Encoder-to-motor gearing ratio can be adjusted.
- In the case of geared setup, the uncertainty of the motor or the frame angle detection at startup can be removed with the help of 2nd IMU.
- Option to enable Briefcase position auto-detection on-the-fly when in 'Follow' mode: just hold the camera by hand and turn frame ±90 degrees.
- More reliable soft limits; option to enable/disable them for each motor independently.
- Back-EMF compensation is applied at full battery voltage amplitude. It allows getting the maximum speed from the motor (that is limited by the Kv parameter of a motor) even with the low 'POWER' setting.
Serial API
- CMD_CONTROL command with the extended format allows specifying different control modes for each axis.
- CMD_AHRS_HELPER command allows accessing internal IMU attitude in DCM form, to use it in the external system or to replace or correct it by the information acquired from the high-grade external IMU.
2.43b6
- GUIWindows, macOS, Linux
- SimpleBGC_GUI_2_43b6.zip(6Mb20.01.2017)
Release notes
- New GUI tab 'Adjustable variables' to change system parameters remotely in real-time:
- 10 slots for trigger-type controls
- 15 slots for analog-type controls
- New sound model: if 'Beep with motors' option is enabled, gimbal plays various sounds instead of simple beeps.
- New Serial API commands to communicate with external I2C devices
- New Serial API commands to store up to 128 bytes of user data in the EEPROM (may be usefull for third-party GUI or external application developers)
- New RC signal source 'API_VIRT_CH1…32' controlled via Serial API to simplify gimbal control (see examples in the specification)
- PID Auto Tuning should give more precise results because of decreased error threshold
- Better error handling on writing parameters to the board via slow connection.
- (GUI) New menu option to save all profiles into single file. This file can be loaded back by standard 'Load from file…' command
- (GUI) New menu option to write all profiles to the board.
- Updated examples for Arduino: SBGC_Serial_API_Examples.zip(27Kb24.08.2015)
- (GUI) New command to backup/restore whole EEPROM (including all calibrations)
- Analog joystick auto-detection: if signal at startup is outside +-50 of neutral point, analog input is disabled. Option can be enabled in the RC tab.
2.43b9
- GUIWindows, macOS, Linux
- SimpleBGC_GUI_2_43b9.zip(6Mb14.04.2015)
- User ManualEnglish
- SimpleBGC_32bit_manual_2_43_eng.pdf(813Kb8.12.2014)
- User ManualFrench (by Nono15)
- SimpleBGC_32bit_manual_2_43_fra.pdf(1Mb26.11.2014)
Release notes
- (GUI): new option to enable auto-detection of system startup in the upside-down mode
- (GUI): New interactive dialog to detect sensor orientation
- (GUI): New interactive dialog to calibrate sensors
- Second UART port to process Serial API commands: Rx goes to RC_ROLL, Tx goes to RC_YAW. It can be enabled in the RC tab ->'RC_ROLL pin mode'
- Spektrum satellite new binding and data format options (used in the 'Bind RC' command and to decode spektrum protocol)
- Bug fixed: in the Follow mode when the camera is pitched down about 90 degrees, its not controlled by YAW
- Bug fixed: calibration of accelerometer in the simple mode did not reset extended mode calibration, making a result of simple calibration not correct.
- Bug fixed: 'Estimate angle from motors' doesnt work in 2.43b6
- Minor bug fixed with firmware update dialog.
- Recovery firmware works now with USB connection on v.3.1 'Tiny' boards.
2.42b7
- GUIWindows, macOS, Linux
- SimpleBGC_GUI_2_42b7.zip(5Mb14.04.2015)
- User ManualEnglish
- SimpleBGC_32bit_manual_2_42_eng.pdf(768Kb5.09.2014)
Release notes
- Bug fixed: in Follow mode, when ROLL is locked, 'INIT.ANGLE' has no effect.
- New command LOOK_DOWN: Camera pithes down to 90 degree with the speed configured in the RC tab.
- New command HOME_POSITION: Camera goes to home position (set by INIT.ANGLE for each axis) with the speed configured in the RC tab.
- Add a 4-second delay after the 'Upside-down mode' command is switched, to let to rotate gimbal to new position.
- (GUI) New option 'Remember last used profile', to make the profile (activated by RC or menu button) default. If disabled, system always starts with profile set as default from the GUI.
- (GUI) Firmware upgrade now works under Mac OS and Linux (see User manual for details)
- (GUI) Option to log realtime data to CSV file for further analysis
2.42b6
- GUIWindows, macOS, Linux
- SimpleBGC_GUI_2_42b6.zip(5Mb14.04.2015)
Release notes
- 4xPWM servo output with adjustable rate to output virtual channels decoded from RC input, or driven by Serial API
- PID auto-tuning
- Adaptive PID gains
- Digital filters to remove resonances: 3 x Notch filters, 2nd-order low-pass filter
- Bug fixed: upside-down settings lost after switching to different profile
- 'Frame upside-down' command now inverts RC control for YAW, together with inverting YAW motor and rotating second IMU
- Bug fixed: should ignore CMD channel during system init
- MOTORS_ON command resets system to home position
- New option for second (frame) IMU: 'Below YAW + PID source'. It means, if Frame IMU is mounted below YAW motor, it can be used as data source for PID controller, and in some cases can give better result, than main IMU.
- (GUI) UI elements re-arranged to adopt new settings and make groupping more consistent
- (GUI) Separate LPF setting for RC and Follow Mode
- (GUI) New setting 'RC Inverse' (you can use it or switch Min. and Max. angles, as before)
- Last used profile is saved as default when switched by service button, RC CMD command of from GUI.
- Bug fixed: s-bus fast mode was not decoded correctly
2.41b4
- GUIWindows, macOS, Linux
- SimpleBGC_GUI_2_41b5.zip(5Mb14.04.2015)
- User ManualEnglish
- SimpleBGC_32bit_manual_2_41_eng.pdf(620Kb26.06.2014)
Release notes
New features
- New button command 'Frame upside-down'. Use it to quickly re-configure system for new frame position (YAW motor is inverted, second IMU orientation is updated).
- 'Beep by motors' option: motors emit sound instead of internal buzzer, when motors are energized.
- Lost of synchronization detection:
- better recovery from this mode
- notification by LED and buzzer (enable 'Errors' checkbox in the 'Service' tab)
- Smooth motor start at power-on
- Option to disable RC limits in SPEED mode (set min=max)
- Improved PID and IMU algorithms lets to achieve precision +-0.06 degree in dynamics, +-0.02 degree in static
- Stable work at bigger ROLL angles (system keep stability up to +-80 degree for ROLL inclination)
- Short beep on each press of menu button (if buzzer confirmation mode is enabled in GUI)
- (GUI) New extended debug variables RMS_ERR_X, FREQ_X helps to detect problems caused by oscillations
- (GUI) New 'Erase EEPROM' menu command
- (GUI) Profile name is stored in the board after renaming. Max. 48 ASCII characters allowed (or less, if national characters used)
- (GUI) New option in the RC tab: 'INIT.ANGLE' to set initial angle of the camera at system startup, if RC control is not applied.
Changes in settings (you need to take it into account when using profiles, saved for previous version)
- Follow speed rate is decreased 4x times, range is increased to 0…255, to make adjustments finer.
- Range for I setting was increased 2x times (old 0.01 equals new 0.02).
- Range for P, D setting was increased 4x times (values will be updated automatically after upgrading).
- Upper limit for PID values increased to 255 (2.55 for I).
- Upper limit for RC speed was increased to 255 and its effect was decreased 4x times to get finer step in adjustment.
Bugfixes
- Changing sensor orientation in GUI does not reset calibration data.
- Fixed problems with RC control in Follow mode and Follow<->Lock transition.
- Battery voltage sensor drifting with time issue was fixed (but may be required to re-calibrate it).
- Bugfix: calibrate poles and direction did not work as expected.
- Add UART parity setting auto-detection from firmware side. Together with GUI auto-detection, it allows to connect Bluetooth modules with Parity=No|Even (but with Parity=No, module doesn't allow to upgrade firmware).
- PID distribution between motors is more correct when frame is picthed and if ROLL and YAW motors differs a lot.
- Bug with the Serial Control fixed (board hangs after first command sent via Serial API).
- IMU: better handling of corrupted sensor data (wrong calibration, vibration, accelerated motion, etc.) and faster reach of settle point.
/! macOS Users Notice
Always check that you have installed the latest version of the driver for a virtual COM port. You can download it by this link.
There is a known problem with the MAC OS 10.13 'High Sierra' - it does not load driver automatically on demand. If you cannot find a COM port where board is connected, in the 'Connection' list in the GUI, try to load the driver manually using the Terminal (go to Applications > Utilities > Terminal in Finder):
Alex Driver Download Windows 7
Then restart GUI and check the Connection list again.
Alex Driver Download Free
This problem will be solved later by new drivers.
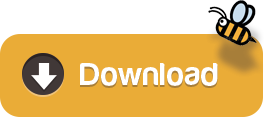